“Our mixed reality R&D has recently entered the stage of verification and commercialization. This is the most important piece of puzzle for our digital transformation at Dolomann Technology with air compressors as our main product.” As soon as Mr. Chen, the chair of Dolomann Technology, took his seat, he shared his research project in cooperation with National Taipei University of Technology with excitement. However, we were quite confused that, as an air compressor agent and manufacturer, what is the relationship between Dolomann and AR/AI? Let us first put these doubts aside, as Mr. Chen shifted to the next, more shocking topic. He said, “Air compressors are the second most energy-consuming equipment in industrial manufacturing, only preceded by air conditioners, but air compressors are not emphasized in Taiwan, only because it is considered a totally traditional industry.”
However, air compressors are highly common and indispensable in the industrial field, and can be found in all industrial manufacturing factories, such as those involving semiconductors, CNC lathes, plastic injection, food processing, and even hospitals and long-term care centers. Interestingly, no matter what kind of factory it is, air compressors are usually installed in the distant corner, because it is the noisiest and hottest machine. If we examine it from the education system of professional development, air compressor is at best a part of a textbook chapter in the department of mechanical engineering. It will be taught during a few classes in the semester, and that is it. Compared with its impact on energy consumption, its significance in the education system is truly disproportional. Demanding work environment, insufficient acknowledgement at school, and the declining birth rate have all led to the loss of talents in related industries, and it would only become worse if there is no intervention.
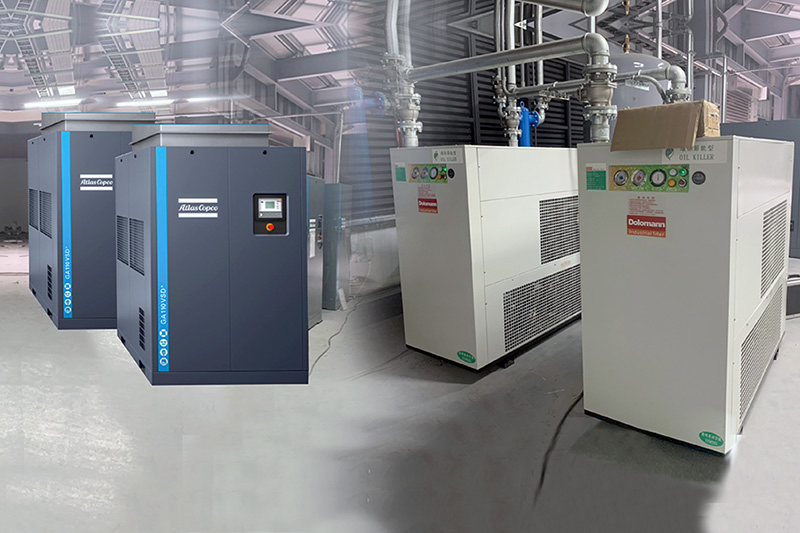
Even so, Mr. Chen still had the passion to change their air compressor products and even the entire industrial ecology. Starting from small air compressors, this experienced business owner who has worked hard in the industry for 30 years gave us a lesson of “Introduction to Air Compressors”. In just one hour, he told us the complete blueprint he devised, and introduced what changes technology (such as AI and mixed reality) can bring to traditional industries.
A set of air compressor installed in an industrial plant has many parts. In addition to the core compressor, there are also compressed air storage tank, dehumidifier, front and rear filters, as well as additional equipment depending on requirements. That is why the whole set of air compressor would usually take up about the space of a classroom. The most critical of these is of course the compressor itself, which not only determines the energy consumption, but also directly affects the quality of the compressed air it produces. In order to maintain the working quality of the compressor and prolong the life of the machinery, lubricant must be added to the compressor, but the lubricant gas mixed in the air during the compression process may cause damage to the other machines that use the compressed air at the end, or affect the manufacturing quality (e.g., in a semiconductor clean room). Thus, it is necessary to use filters, electrostatic adsorption, and other measures to purify the air as much as possible, both before and after compression.
Compared with the lubricant-type compressor, there is also the lubricant-free compressor, which uses metal processing technology to add a coating to the surface of the turbine blade, and try to control the machinery’s working temperature and intervals. Under an ideal condition, since this type of compressors do not need lubricant, the purity of the compressed air would be higher than that of a lubricant-type compressor, but it is achieved at the cost of higher energy consumption.
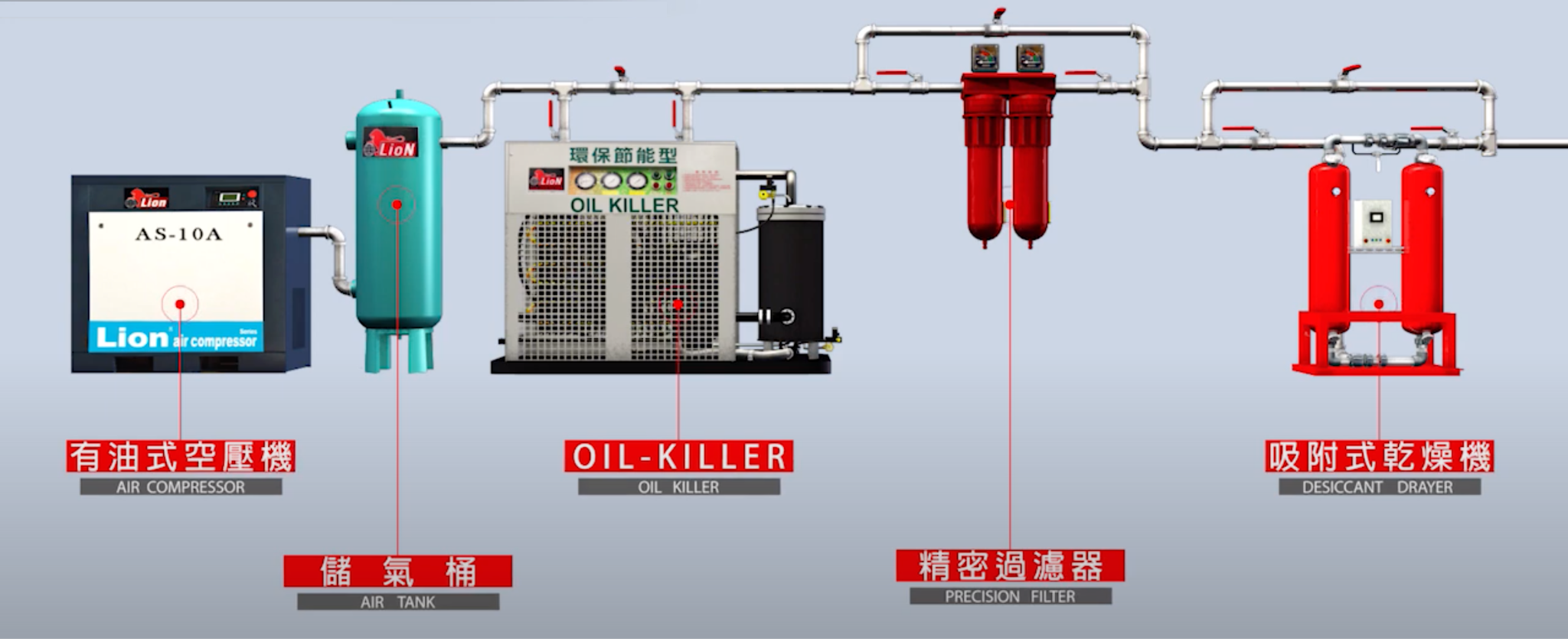
How to improve the quality of the compressed air produced was the first research topic for Dolomann. They needed to figure out how to achieve “lubricant-free-level purification” on the lubricant-type compressor with the same, or even better, quality. Using the principles of condensation, drying, oil-gas separation, and filtration, the OIL-KILLER air compressor model, equipped with a low-temperature purifier, can achieve the effect of air cleaning and oil separation, allowing the oil-gas and water-gas in the air pipeline to be filtered, and truly achieve oil-free and water-free results. Only this top quality can meet the increasingly sophisticated industrial process requirements nowadays.
After the lubricant-free purification technology was patented, it became the niche of Dolomann Technology, but Mr. Chen did not stop there. Keeping up with the global Industry 4.0 trend, he further underwent the smart transformation process for the filtration system, and developed the human-machine interface in order to manage the overall energy efficiency and carry out information exchange with the cloud system through the connection of sensors. The purification-related data can be transmitted to the mobile phone so that users can monitor energy consumption and purification quality at any time.
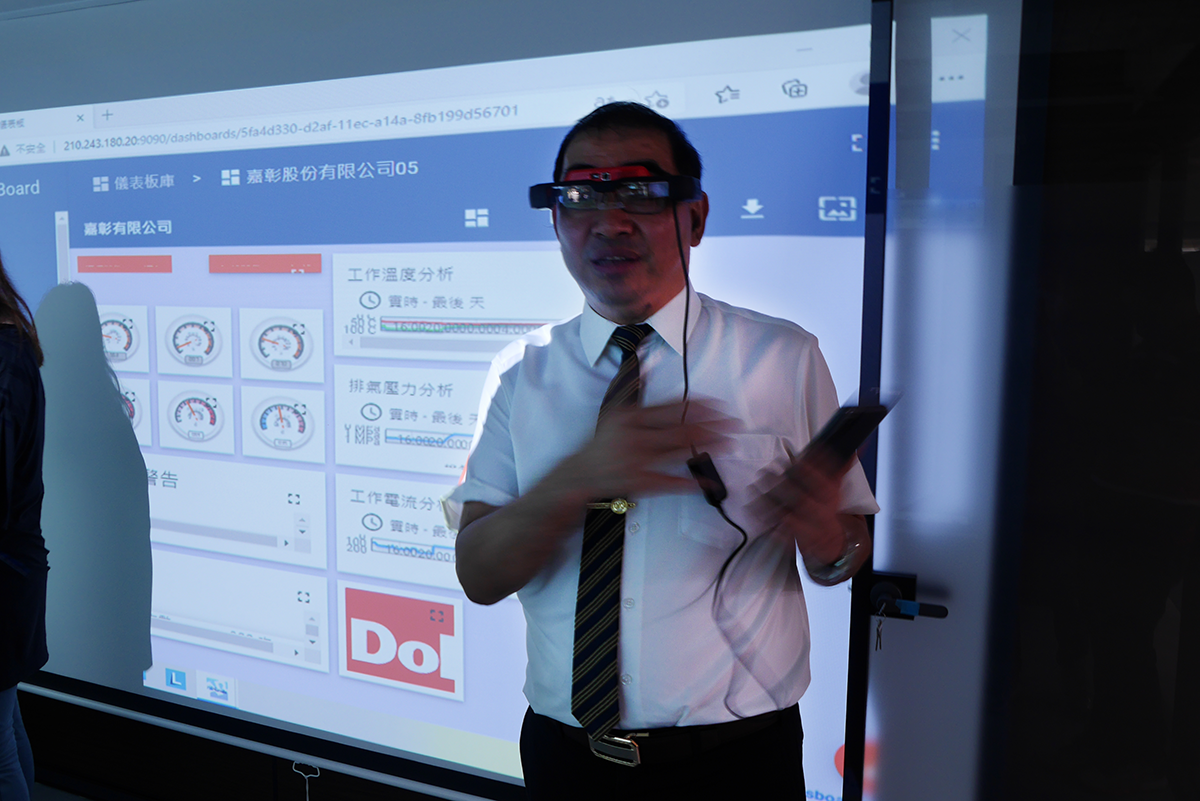
Mr. Chen put on the AR glasses and sat in the information room he built, talking eloquently about the real-time information of various air compressors projected on the wall with pride. Although the technology and air compressor products of Dolomann already have a place in the market, it is still difficult to complete the industrial innovation with their own resources. “For me, this is like starting a business from scratch again. There are many problems to be overcome, and I have to re-learn a lot of stuff.”
For a traditional industry completely unfamiliar with information technology, it is not easy to go through digital transformation. However, with the assistance of the IoT Service Hub, the problems were resolved one by one, and the blueprint devised by Mr. Chen gradually became reality. “When we first started to make air compressors smart, we could only find ready-made IoT modules on the market, which are too powerful and expensive, but we actually do not need all those high-end functions.” Air compressor is not a very complicated machine, and not too many sensors are needed. Instead, it only needs the basic network communication functions, so it was difficult to find a chip model that is small and answers these requirements.
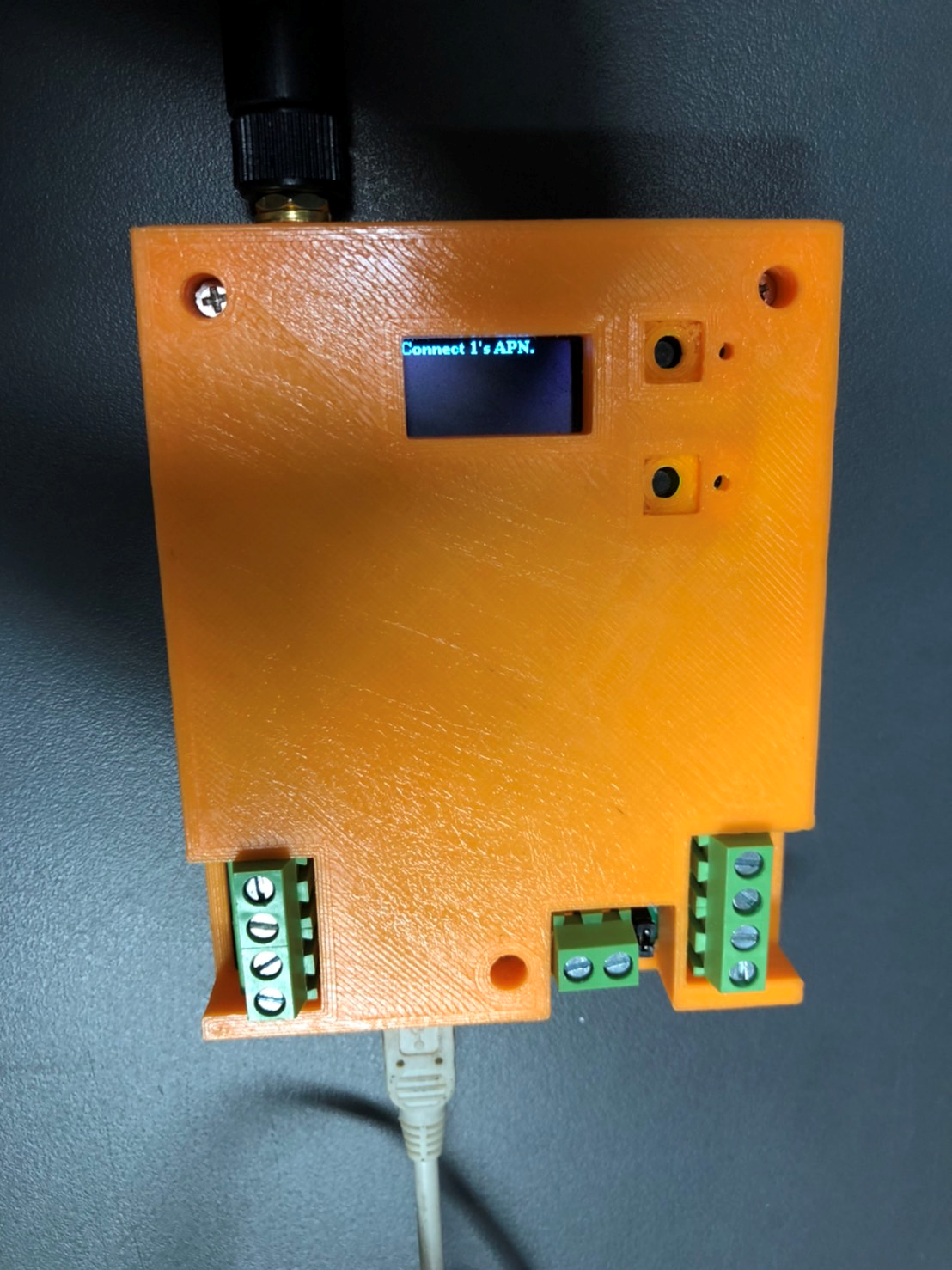
Through the assistance of YouLight Technology, a smart manufacturing consultant at the IoT Service Hub, the domestic IC development EVB DSI2598+ was introduced to create an exclusive smart module for air compressor. What was more, YouLight Technology also provided overall suggestions for Mr. Chen’s business blueprint. For example, it recommended Dolomann Technology to connect to Chunghwa Telecom’s hiRemote data management platform for data storage, to use open source software for data calculation, and to look for “MIT” high-quality AR glasses. All these helped Mr. Chen realize his business blueprint.
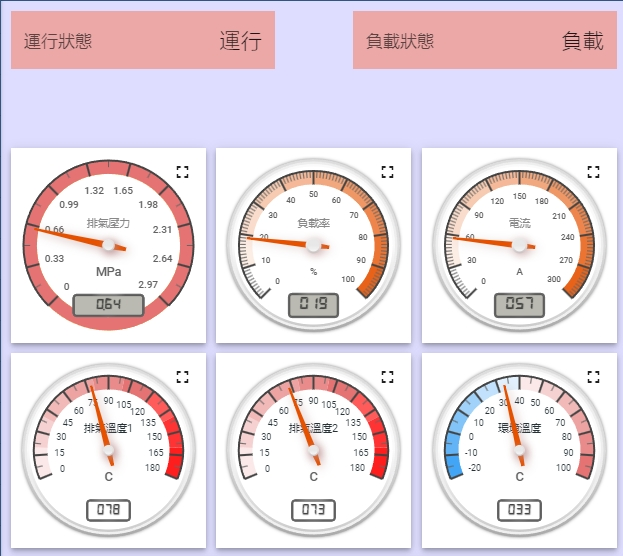
With this air compressor information system, it is possible to continuously monitor the working quality of air compressors and collect the data of different types of air compressors through the sensors and IoT modules installed. After analysis, the results can facilitate the early warning alert system before possible damage or malfunctioning occurs. Factories can thus plan maintenance and repair schedules in advance, and avoid temporary shutdowns which might cause damage to other machines on the production line. The production capacity can also be guarded at all times.
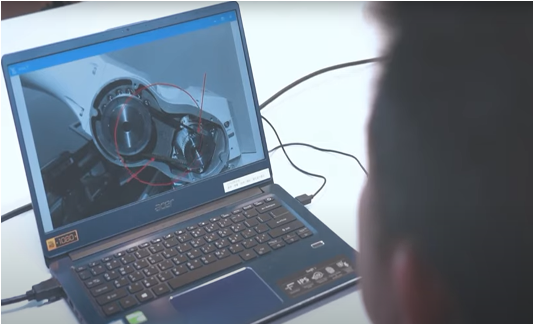
The application of AR can effectively solve the problem of labor power shortage in the industry. There is a special phenomenon in the air compressor industry, which is the fact that there are often multiple air compressors of different brands in the same factory. For maintenance personnel, it is a big challenge to be proficient in various types of brands and models. To solve this, the AR solution introduced by Dolomann can remotely connect on-site maintenance personnel with senior consultant mechanics; through the camera of on-site personnel, the captured pictures are sent to the online maintenance consultant, who can directly examine the machine and identify the problems. At the same time, the senior consultant can also tell the on-site maintenance personnel what to do step by step. In this way, the maintenance resources can be streamlined to cope with diminishing labor power.
There have always been many challenges in the transformation of traditional industries, but the experience of Dolomann’s active engagement has proven that as long as business owners clearly understand the problems encountered, adopt the most appropriate solutions, and seek consulting resources (e.g., the IoT Service Hub), the end results will be more than satisfying!